Tecasint 2021
TECASINT 2011 is unfilled, while TECASINT 2021 contains 15% graphite which offer improved wear resistance and a lower coefficient of friction. TECASINT 2000 series with their superior physical properties, are ideal for application in the aerospace, nuclear, automotive, electrical/electronics, and chemical processing industries. Improved sliding properties due to 15w% graphite. The electrical conductivity is also better comparing to the natural Tecasint 2011. Series of Tecasint 2000: have very high modulus, high rigidity, but compared to series of 1000 reduced moisture adsorption beside higher toughness and machining capability. Tecasint 2021, Vespel SP-21, Duratron PI D7015G Filler 15% Graphite Color Black Density (g/cm^3) 1.46 D 792 Mechanical. Property Value Typical ASTM Test; Modulus of Elasticity (Tensile Test) (psi) 638000.

Ensinger’s Tecasint® family and DuPont’s Vespel® family of high-performance polyimide resins out perform most engineering thermoplastics in thermally aggressive bearing and seal applications. With or without lubrication these materials function over a wide range of temperatures and stresses while retaining outstanding creep strength, abrasion resistance, and compressive strength. Their superior thermal resistance allows them to carry loads at temperatures beyond the reach of most plastic materials and do so while exhibiting extremely low creep.
The extraordinary properties of Tecasint® and Vespel® make them the optimal choice for thermally aggressive applications in the automotive, off-road vehicle, jet engine and semiconductor manufacturing sectors. Polyimides do not become brittle, even at -400° F and have continuous service temperatures approaching 600° F. Close tolerance machining can be achieved with standard metal-working equipment with experience, however special techniques are employed to achieve extremely close tolerances and surface finishes less than 10 rms. Typical applications include sleeve and flanged bearings, rotary seal rings, wafer guides and carriers, insulators, valve seats, gaskets and thrust washers.
Grades
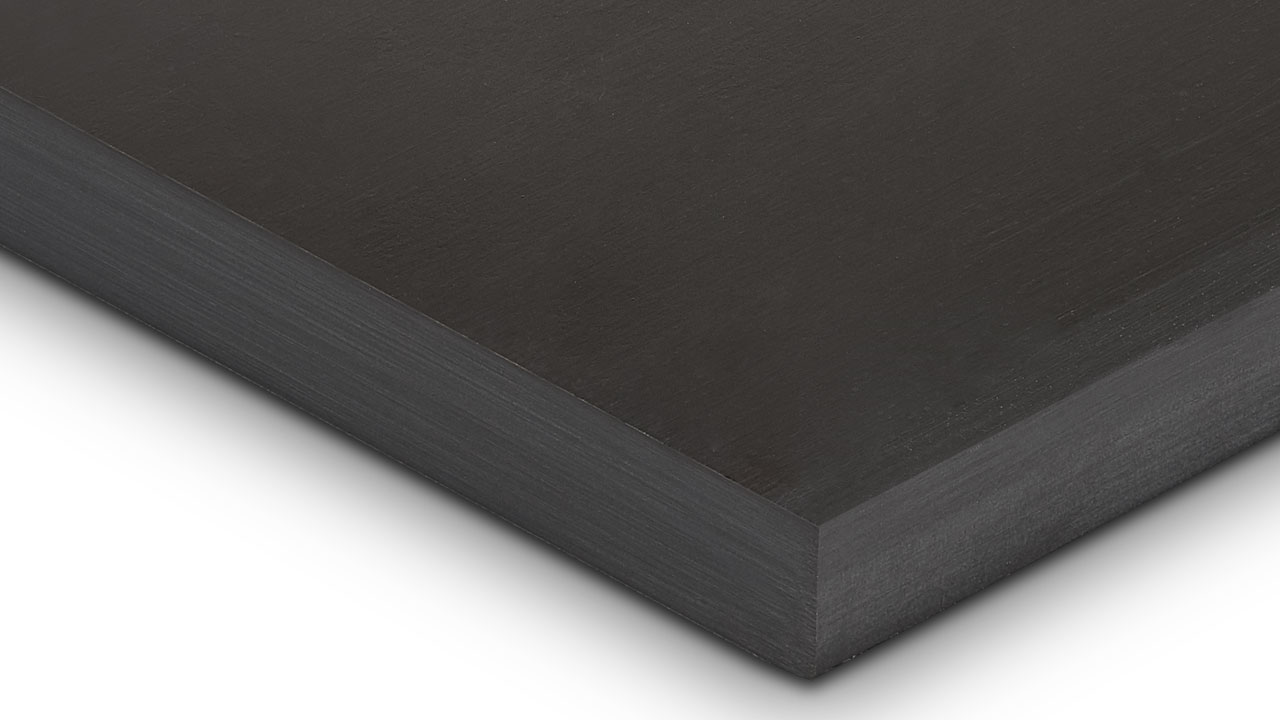

Bearing Grade Polyimides most commonly used as bearing and wear components are;
Tecasint® 2021, Vespel® SP-21, where 15% graphite by weight is added to the base resin for increased wear resistance and reduced friction in applications such as bearings, thrust washes, bushings, seal rings, slide blocks and other wear surfaces. These have the highest mechanical properties of the graphite-filled grades.
Tecasint® 2031, Vespel® SP-22, where 40% graphite by weight is added to the base resin for enhanced resistance to wear and friction and good dimensional and oxidative stability. These have the lowest coefficient of thermal expansion of the graphite-filled grades.
Vespel® SP-211, where 10% Teflon (PTFE) and 15% graphite by weight are added to the base resin for the lowest coefficient of friction over a wide range of operating conditions. Vespel® SP-211 has excellent wear resistance up to 300° F.
Vespel® SP-3, where 15% molybdenum disulfide by weight is added to the base resin for bearing and wear components in vacuum and moisture-free environments.
Tecasint® is a registered trademark of Ensinger, Vespel® is a registered trademark of E.I. Dupont
Specifications for Tecasint® 2031 and Vespel® SP-22 (40% Graphite Filled Polyimide) | Test | Value | Units |
Specific Gravity, 73°F | D792 | .0596 | Lb/in.3 |
Tensile Strength @ Yield, 73°F | D638 | 9430 | psi |
Tensile Modulus of Elasticity, 73°F | D638 | psi | |
Tensile Elongation (at break), 73°F | D638 | 2.2 | % |
Flexural Strength, 73°F | D790 | 12700 | psi |
Flexural Modulus of Elasticity | D790 | 755.2 | ksi |
Shear Strength, 73°F | D732 | psi | |
Compressive Strength – Ultimate | 16,300 | psi | |
Compressive Strength at 2% Deformation | D695 | 6,000 | psi |
Compressive Strength at 10% Deformation | D695 | 16,300 | psi |
Deformation Under Load | % | ||
Compressive Modulus of Elasticity, 73°F | D695 | 294 | ksi |
Compressive Strength ⊥ to Laminate (Modulus) | psi | ||
Compressive Strength ⊥ to Laminate (Yield) | psi | ||
Compressive Strength ⊥ to Laminate (Ultimate) | psi | ||
Hardness, Durometer (Shore “D” scale) | D2240 | 84 | |
Hardness, Rockwell (Scale as noted) | D785 | Rockwell M | |
Izod Impact, Notched @ 73°F | D256 Type A | 1.57 | ft.lbs/in. of notch |
Coefficient of Friction (Dry vs Steel) Static | PTM55007 | .27 | |
Coefficient of Friction (Dry vs Steel) Dynamic | PTM55007 | .2 | |
Maximum Static Bearing Load (P) | PTM55007 | 6,000 | psi |
Maximum Unlubricated No Load Bearing Velocity (V) | PTM55007 | 1,000 | ft/minute |
Maximum Limiting PV (Unlubricated) | PTM55007 | 300,000 | psi x ft/min. |
Wear Factor “K” x 10-10 | PTM55010 | Cubic in.-min/ft.lbs.hr | |
Sand Wheel Wear/Abrasion Test | UHMW=100 | ||
Minimum Mating Surface Hardness | Rockwell (Brinnell) | ||
Coefficient of Linear Thermal Expansion | E-831(TMA) | 1.67 | in/in/°F x 10-5 |
Coefficient of Thermal Expansion // to Laminates | E-831(TMA) | 1.67 | in/in/°F x 10-5 |
Coefficient of Thermal Expansion Perpendicular to Laminates | E-831(TMA) | 1.67 | in/in/°F x 10-5 |
Softening Point | °F | ||
Heat Deflection Temperature 264 psi | D648 | 613 | °F |
Embrittlement Temperature | <400 | °F Min. | |
Continuous Service Temperature in Air | 572 | °F Max. | |
Short Term Service Temperature | 600 | °F Max. | |
Tg-Glass Transition (Amorphous) | D3418 | 698 | °F |
Melting Point (Crystalline Peak) | D3418 | N/A | °F |
Thermal Conductivity | F433 | 12.0 | BTU-in/(hr/ft2°F) |
Dielectric Strength Short Term | D149 | Volts/mil | |
Volume Resistivity | D257 | 1012-1013 | ohm/cm |
Surface Resistivity | D257 | ohm/cm | |
Dielectric Constant, 106 Hz | D150 | ||
Dissipation Factor, 106 Hz | D150 | ||
Flammability @ 3.1mm(1/8 in.) UL94 | UL94 | V-0 | |
Arc Resistance | seconds | ||
Water Absorption, Immersion 24 Hours | D570 (2) | 1.2 | % |
Water Absorption, Immersion Saturation | D570 (2) | 2.1 | % |
Machinability Rating | 5 | 1=easy, 10=difficult | |
Rod Diameter Availability (Call for Availability) | 1 | 3 | inches |
Sheet Thickness Availability (Call for Availability) | .25 | 2 | inches |
Tecasint 2021 Mercedes
Characteristics / Attributes | Superior Temperature & Chemical Resistance, Highest PV Rating, Excellent Bearing and Wear Properties, High Cost |